$275 million commitment to brew better molecules for manufacturing
The Department of Defense and dozens of private companies hope to jump-start the nation's bioeconomy
October 20, 2020
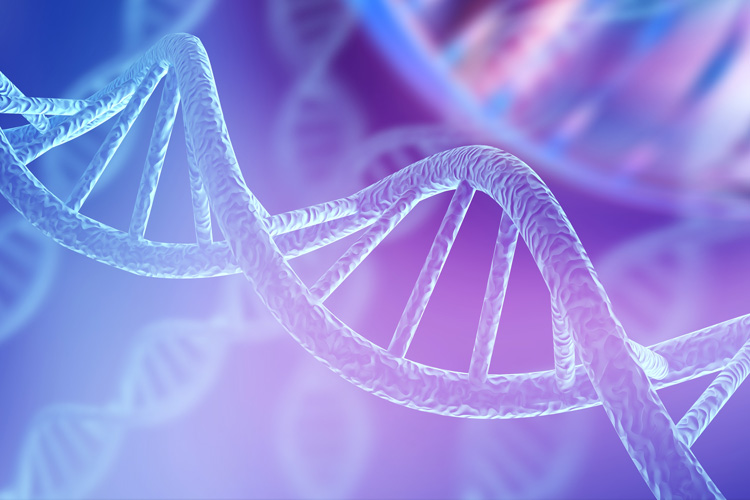
By inserting novel genes into bacteria or yeast, scientists can make them produce a huge range of chemicals of use in industry. A new initiative funded by the U.S. Department of Defense, private companies, universities and non-profits seeks to scale up these capabilities to produce large and inexpensive quantities of biomolecules to ramp up the nation’s bioeconomy.(iStock image)
The U.S. Department of Defense and more than 80 companies, universities, states and research institutes will invest at least $275 million over the next seven years to scale up the microbial production of biomolecules. The effort will enable a growing biomanufacturing industry to supply a broad range of businesses with large quantities of chemicals at the low prices necessary to make them competitive with petroleum-based alternatives.
Biomolecules on the market today are mostly drugs or fragrances made by small batch fermentation in yeast or bacteria, a process much like that of a craft brewery. The goal of the public-private partnership, the Bioindustrial Manufacturing And Design Ecosystem (BioMADE), is to employ the same principles of genetic engineering and engineering biology used in the pharmaceutical industry to produce chemicals other than drugs on a scale similar to that used to ferment corn into ethanol for transportation. The new bioindustrial manufacturing innovation institute was announced today (Oct. 20) by the Department of Defense (DoD).
“You can make almost any molecule now in small quantities using engineering biology approaches. The capabilities are incredible,” said Douglas Friedman, the CEO of BioMADE and executive director of the Engineering Biology Research Consortium (EBRC), a large public-private partnership focused on engineering biology that is based at the University of California, Berkeley.
“But for commercial products, typically we want to make them in large quantities that are then used to create polymers, materials, films, paint and countless other products. The question today is: How do you transition from making anything in small quantities to making anything in commercial quantities? What we need is to be able to predictably take these engineered microbes and put them in a 100,000-liter fermentation tank and make tons of material, and that we can’t do.”
BioMADE will be seeded by $87.5 million in federal funds during the first five years, matched by more than $180 million from non-federal sources.
“BioMADE is meant to be a permanent institute. We have seven years to prove that we can bring the industry together to create an ecosystem that can develop the cutting-edge sustainable technologies that industry needs to be able to make products that they can sell,” Friedman said. “The institute itself is not in the business of making products for the market, but about developing technology and making it available to member companies so that they can then build their own products.”
BioMADE is the eighth Department of Defense (DoD)-sponsored Manufacturing Innovation Institute (MII) and the 16th institute in the Manufacturing USA network, a federally-driven effort to secure America’s future through manufacturing innovation, education and collaboration. The biomanufacturing institute aims to make the country more reliant on domestic chemicals and to make these chemicals more environmentally friendly and sustainable. An added benefit, Friedman said, is that, because biomanufacturing is done on a smaller scale than is typical of oil-based chemical manufacturing, production can be distributed throughout the country, not just near sources of crude oil.
“The Department of Defense is committed to promoting U.S. biotechnology innovation and securing America’s bioindustrial base. Through today’s award, we are pleased to work with new partners to accelerate the department’s biotechnology modernization and the development of this field, which is so critical to our nation’s future security and prosperity,” said Michael Kratsios, U.S. acting under secretary of defense for research and engineering.
The institute will be headquartered at the University of Minnesota, St. Paul, with major satellites at UC Berkeley and MIT. Also participating will be 30 other universities and laboratories and six non-profits, in addition to 24 community colleges that will help train a workforce in engineering biology and fermentation science.
A new biomanufacturing ecosystem
“We are honored to host BioMADE and believe that this institute will advance a new and significant biomanufacturing innovation ecosystem,” said University of Minnesota President Joan T. A. Gabel. “Our region — the Bold North — is home to 16 Fortune 500 companies and a highly sought-after educated workforce. We anticipate many future industrial biomanufacturing firms being created here, taking advantage of proximity to the agricultural raw materials needed for their production, the depth of talent we offer and the business infrastructure that already serves related firms like Cargill, General Mills, CHS and Land O’Lakes.”
For over a century, Friedman noted, the U.S. has used biology to manufacture products like fuels, including ethanol, and solvents. More recently, products such as lactic acid have led to the development of renewable plastics not dependent on crude oil. Today, a vast array of renewable products produced by the latest advances in engineering biology are entering nearly every sector of the economy.
These biomanufacturing yeast and bacteria are created by inserting genes to create new metabolic pathways that, in effect, force the microbes to produce a molecule they can’t use, but humans can. Grown in fermentation tanks, these genetically engineered organisms are fed sugar and excrete products that are then extracted for use.
One example of a molecule made exclusively with biomanufacturing is the monomer Zymergen developed for the company’s new optical film, Hyaline. Zymergen — an Emeryville-based company that is part of the new institute — developed Hyaline in response to an unmet electronics market need. In this case, that need is to improve optical clarity and scratch resistance on many cell phone and tablet screens.
“The broader BioMADE team will provide proof-of-concept manufacturing capacity and help develop key capabilities in the emerging manufacturing workforce, both of which are critical to strengthening U.S. competitiveness,” said Zach Serber, chief science officer and co-founder of Zymergen.
Another institute member, Amyris of Emeryville, is best known for its anti-malarial drug, artemisinin, produced by fermentation and distributed as part of a combination therapy throughout the tropics. But the company also ferments squalene — a cosmetic ingredient normally sourced from sharks — and even markets a 100% plant-based squalene skin cream, Biossance.
Similar companies have sprung up around the country — in particular, in the Boston area — where many are spinoffs from MIT. BioMADE will link the Boston and Bay Area biotech hubs and biotech companies throughout the U.S. with companies such as Cargill and ADM that have experience with large-scale, but simpler, biomanufacturing.
“The San Francisco Bay Area and the Boston area are major biotechnology innovation hubs in the U.S.,” Friedman said. “What we need to do is connect those innovation hubs — which include companies and the universities around them that can make a small amount of anything — with the Cargills of the world that can make a large amount of a small number of things and solidify those connections in order to develop a much greater number of products.”
One of the molecules DoD is interested in is resveratrol, an ingredient in red wine that also has fire retardant properties when polymerized, making it of interest in the electronics industry. The the food-grade version of resveratrol now available — used mainly in dietary supplements — is too expensive to serve as a polymer source. Bio-based resveratrol would be cheaper and easier to make.
“Bridging the gap between lab-scale and at-scale manufacturing, BioMADE brings together companies, universities, national labs and government to strengthen America’s bioeconomy,” said Friedman.
He noted that UC Berkeley’s long history of research and innovation in engineering biology/synthetic biology allowed the EBRC to assemble the consortium in a way that will benefit a huge array of companies, as well as the country’s workforce and national security.
“We, at EBRC, could not have led this team without the critical insights and involvement of our partner institutions and their commitment to the vision of a thriving public-private solution to advance domestic biomanufacturing,” said Friedman. “Turning to the future, we look forward to an inclusive and comprehensive ecosystem of institutions across the country, unified with the goal of advancing U.S. biomanufacturing capabilities, creating products that are as high performing as they are environmentally sustainable.”